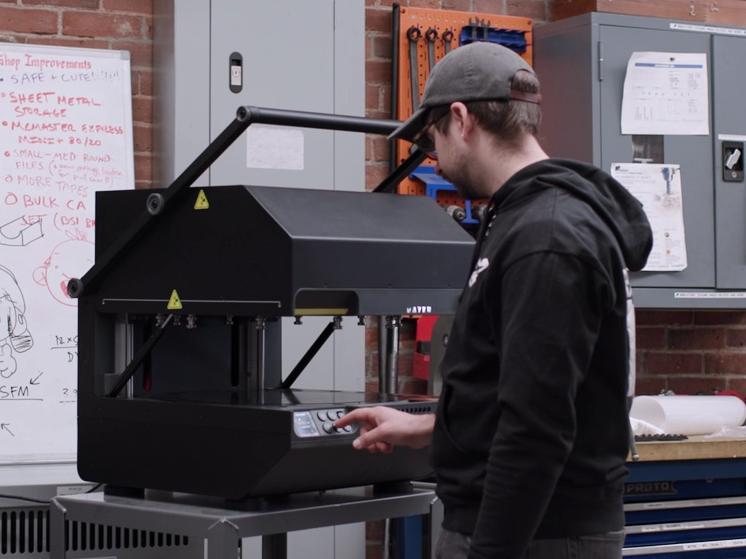
Die Strategie von Formlabs
Formlabs ist bekannt für seine innovativen 3D-Drucklösungen – doch hinter den Kulissen setzt das Unternehmen auf eine klare Strategie: Maximale Unabhängigkeit und Geschwindigkeit im Entwicklungsprozess. Insbesondere bei der Entwicklung des Form 4 – der neuesten Generation von Harz-3D-Druckern – war es entscheidend, schnell und ohne externe Abhängigkeiten zu arbeiten. Ein zentrales Werkzeug dabei: Der Mayku Multiplier, eine kompakte Druckformmaschine für das Inhouse-Thermoformen.
Schlanke, präzise Teile in kürzester Zeit
Beim Bau des Form 4 spielte das sogenannte LPU 4 (Light Processing Unit) eine Schlüsselrolle. Diese Einheit benötigt eine schmale, transparente Abdeckung, die verhindern soll, dass flüssiges Harz eindringt und Sensoren beschädigt. Solch ein Bauteil muss nicht nur dünn, sondern auch mechanisch stabil sein – ein echter Balanceakt bei der Herstellung.
Traditionelle Verfahren wie das Vakuumformen oder externe Fertigungsdienstleister stießen hier schnell an ihre Grenzen: Lange Rüstzeiten, komplizierte Kalibrierung, hoher Material- und Zeitaufwand – all das stand im Widerspruch zu Formlabs’ agiler Produktentwicklung.
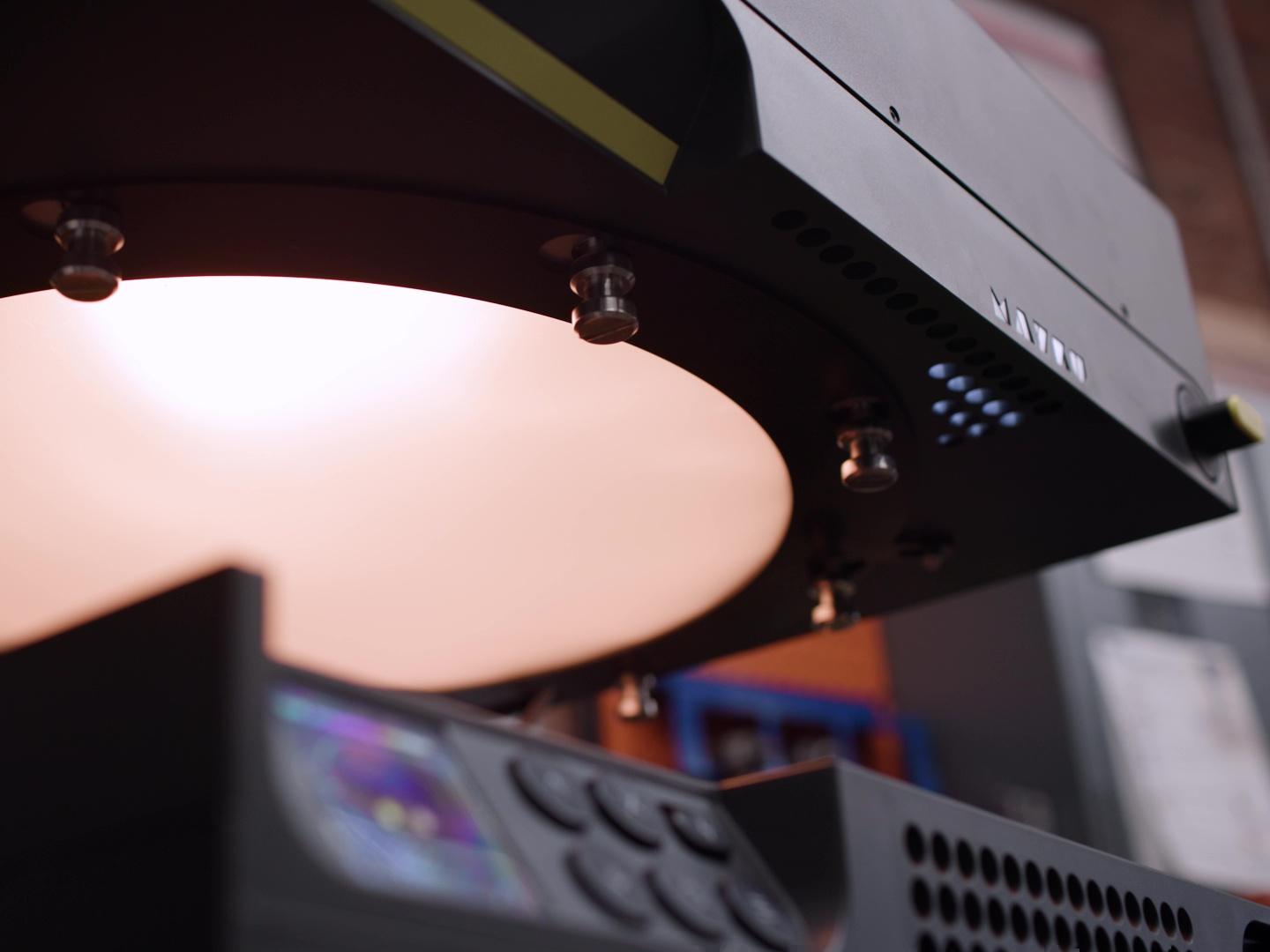
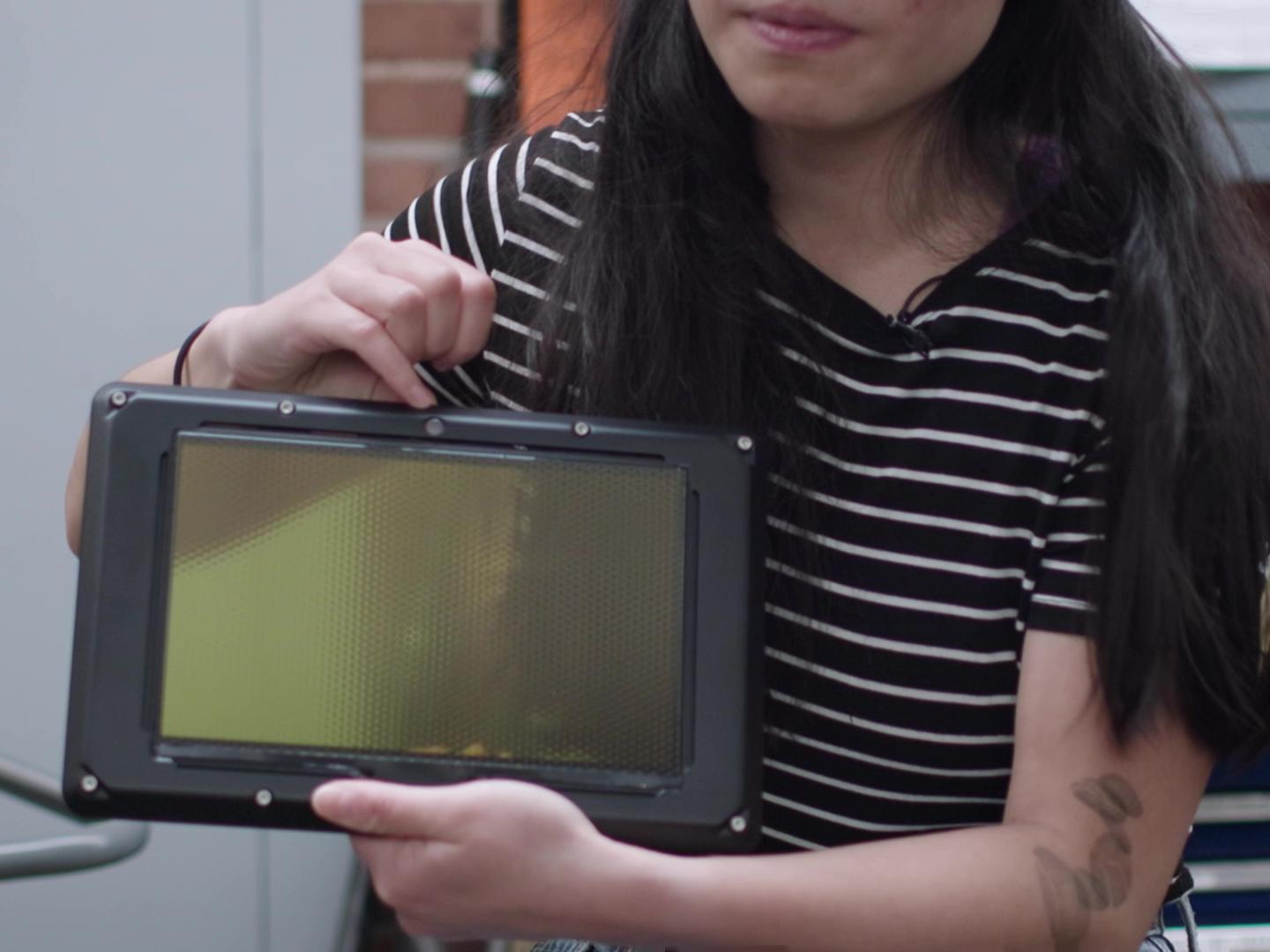
Druckformen mit dem Mayku Multiplier
Der Mayku Multiplier ermöglichte es dem Team, Thermoformteile direkt vor Ort zu entwickeln und zu testen. Die Kombination mit den eigenen Formlabs 3D-Druckern war dabei entscheidend: Formen konnten innerhalb weniger Stunden gedruckt und noch am selben Tag genutzt werden. So wurde aus einem mehrwöchigen Prozess ein Workflow von nur ein bis zwei Tagen.
Franko Kosic-Matulic, Maschinenbaukoordinator bei Formlabs, betont:
„Der Multiplier liefert detailreiche, komplexe Ergebnisse – schnell und zuverlässig. Ohne gute Werkzeuge wird der Inhouse-Prototypenbau oft zur Frustquelle. Der Multiplier beseitigt diese Hürde.“
Von der Idee zum Prototyp in zwei Tagen
Ein Beispiel aus der Praxis: Für die IR-Sensorabdeckung der LPU 4-Einheit wurde ein passgenaues Bauteil benötigt – klein, präzise und stabil. Mit dem Multiplier formte das Team verschiedene Materialoptionen auf selbst gedruckten Formen, testete Varianten und fand in kürzester Zeit die optimale Lösung.
Jennifer Lu, Maschinenbauingenieurin bei Formlabs, bringt es auf den Punkt:
„Von der Idee bis zum Prototyp in ein bis zwei Tagen – das verändert unsere Arbeitsweise grundlegend. Wir testen schneller, lernen schneller und entwickeln so bessere Produkte.“
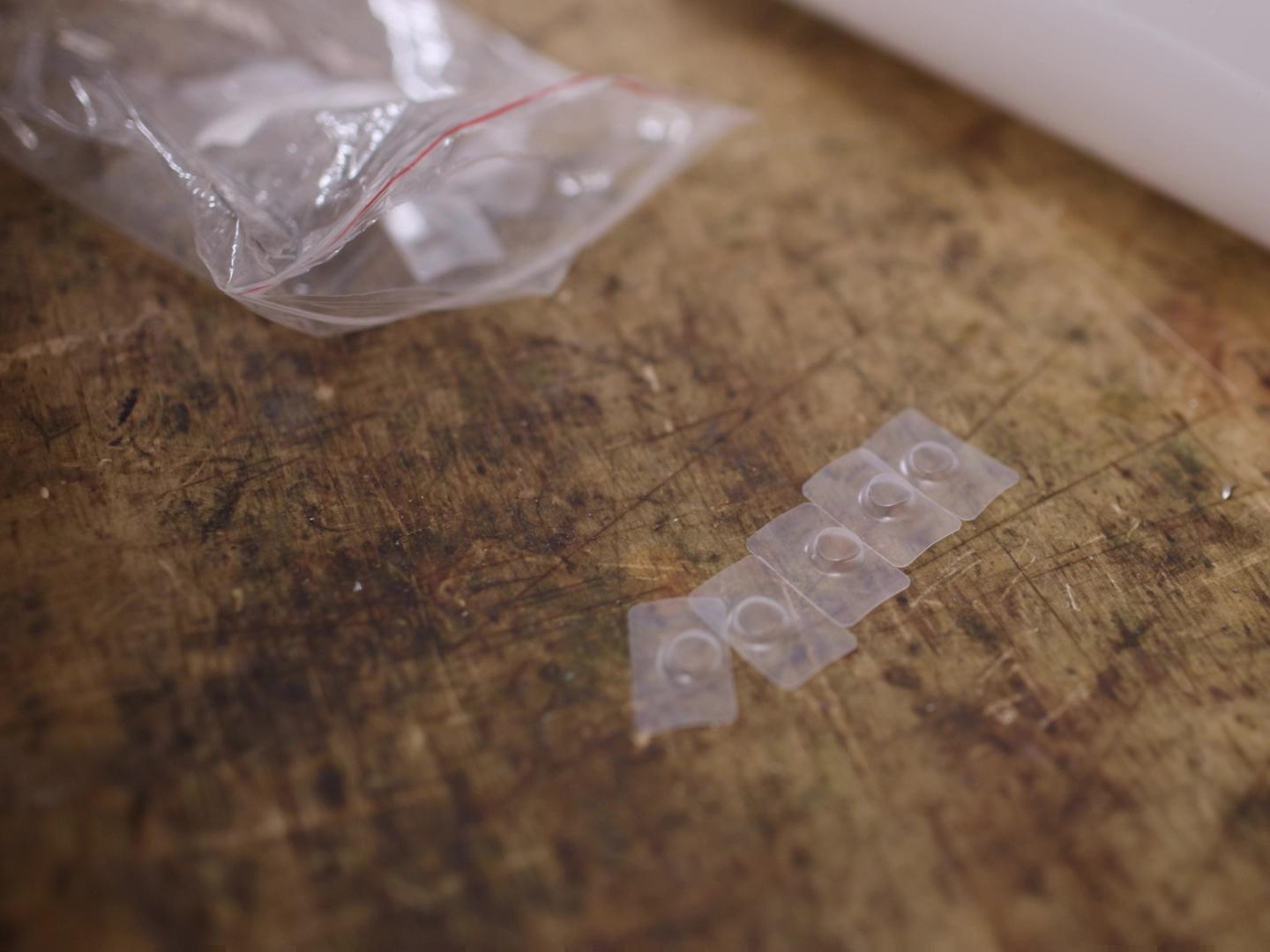
Klassisches Vakuumformen vs. Druckformen mit dem Multiplier
Arbeitsschritt | Vakuumformen | Druckformen mit Multiplier |
Maschinenrüstzeit | 30-60 Minuten | 10 Minuten |
Kalibrierung | ~ 1 Stunde | < 5 Minuten (mit Presets) |
Abkühlzeit | ~ 15 Minuten | ~ 5 Minuten |
Outsourcing vs. Inhouse-Prototyping
Schritt | Outsourcing | Mit Mayku Multiplier |
Formenerstellung | 3 - 7 Tage | 2 - 4 Stunden (3D-Druck) |
Teilefertigung | Bis zu 2 Wochen | Am selben Tag |
Gesamtzeit | 2 - 3 Wochen | 1 - 2 Tage |
Innovation braucht Flexibilität
Der Einsatz des Mayku Multiplier zeigt deutlich, wie wichtig Flexibilität und Schnelligkeit in der Produktentwicklung sind. Durch die Integration der Druckformtechnologie in den eigenen Entwicklungsprozess konnte Formlabs interne Abläufe optimieren, Kosten senken und die Time-to-Market deutlich verkürzen. Der Multiplier ist dabei nicht nur ein Werkzeug, sondern ein echter Innovationsbeschleuniger.
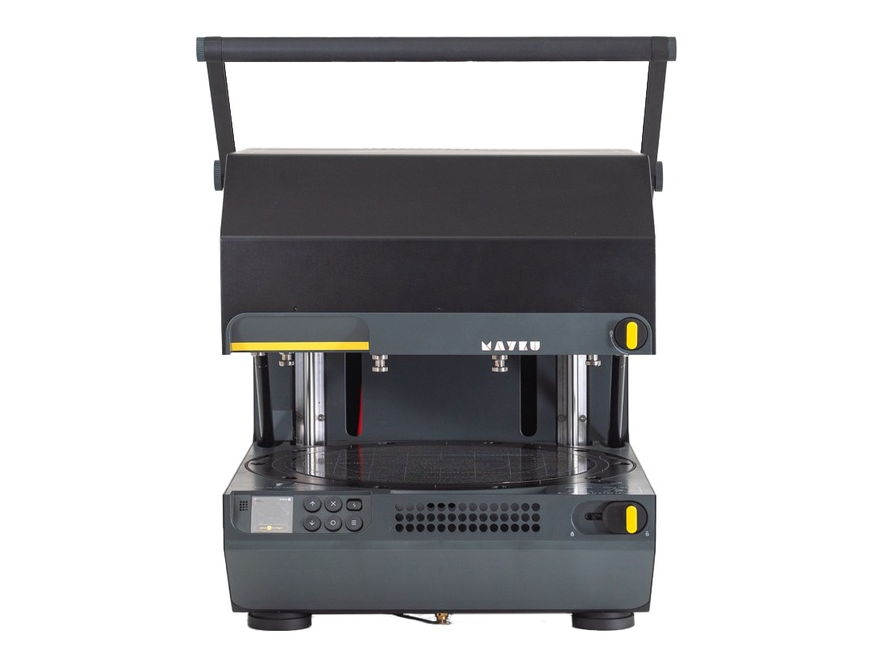